El concreto es un material durable y resistente pero, dado que se trabaja en su forma líquida, prácticamente puede adquirir cualquier forma. Esta combinación de características es la razón principal por la que es un material de construcción tan popular para exteriores.
Ya sea que adquiera la forma de un camino de entrada amplio hacia una casa moderna, un paso vehicular semicircular frente a una residencia, o una modesta entrada delantera, el concreto proporciona solidez y permanencia a los lugares donde vivimos.
Historia del concreto
· Egipto Antiguo:
Los egipcios usaron el yeso calcinado para dar al ladrillo o a las estructuras de piedra una capa lisa.
· Grecia antigua:
Una aplicación similar de piedra caliza calcinada fue utilizada por los Griegos antiguos.
· Antigua Roma:
·El Coliseo Romano
Los Romanos utilizaron con frecuencia el agregado quebrado del ladrillo embutido en una mezcla de la masilla de la cal con polvo del ladrillo o la ceniza volcánica. Construyeron una variedad amplia de estructuras que incorporaron la piedra y concreto, incluyendo los caminos, los acueductos, los templos y los palacios.
Los Romanos antiguos utilizaron losas de concreto en muchas de sus estructuras públicas grandes como el Coliseo y el Partenón. El concreto también fue utilizado en la pared de la defensa que abarca Roma, más muchos caminos y los acueductos que todavía existen hoy. Los Romanos utilizaron muchas técnicas innovadoras para manejar el peso del concreto. Para aligerar el peso de estructuras enormes, encajonaron a menudo tarros de barro vacíos en las paredes. También utilizaron barras de metal como refuerzos en el concreto cuando fueron construidos techos estrechos sobre callejones.
·1774 - El Faro de Smeaton
John Smeaton había encontrado que combinar la cal viva con otros materiales creaba un material extremadamente duro que se podría utilizar para unir juntos otros materiales. Él utilizó este conocimiento para construir la primera estructura de concreto desde la Roma antigua.
"John Smeaton, uno de los grandes ingenieros del siglo dieciocho, logró un triunfo al construir el faro de Eddystone en Inglaterra. Los faros anteriores en este punto habían sido destruidos por las tormentas y el sitio estaba expuesto a la extrema fuerza del mar. Pero Smeaton utilizó un sistema en la construcción de su cantería que la limita junta en un todo extremadamente tenaz. Él bloqueó las piedras unas en otras y para las fundaciones y el material de junta utilizó una mezcla de la cal viva, arcilla, arena y escoria de hierro machacada – concreto, eso es. Esto ocurrió en 1774... [y] es el primer uso del concreto desde el período romano." (Citado de Espacio, Tiempo y Arquitectura: el crecimiento de una nueva tradición, por Sigfried Giedion, Harvard University Press, 1954. Aguafuerte del informe de Smeaton sobre el faro, una narrativa del edificio y una descripción de la construcción del faro de Eddystone.)
·1816
El primer puente de concreto (no reforzado) fue construido en Souillac, Francia.
·1825 - Paso del canal
El primer concreto moderno producido en América se utiliza en la construcción del canal de Erie. Se utilizó el cemento hecho de la "cal hidráulica" encontrada en los condados de Madison en Nueva York, de Cayuga y de Onondaga.
Primero llamado "La zanja de Clinton", el canal de Erie se abrió en 1825. Fue un instrumento en la apertura de la expansión a través de la región de Los Grandes Lagos. Su éxito comercial fue atribuido a menudo al hecho de que el coste de mantenimiento de los pasos de concreto era muy bajo. El volumen del concreto usado en su construcción le hizo el proyecto de construcción de concreto más grande de sus días.
·1897
Sears Roebuck ofreció el artículo #G2452, un barril de "Cemento, natural" en $1,25 por barril y el artículo #G2453, "cemento Portland, importado" en $3,40 por barril de 50 galones.
·1901 - Abrazadera de columna
Arthur Henry Symons diseñó una abrazadera de columna que se utilizaría con las formas de concreto trabajo – construidas.
Arthur Henry Symons diseñó una abrazadera de columna para encofrado de concreto en su departamento de herrero en la ciudad de Kansas. Era ajustable y mantenía las formas cuadradas, dos características apreciadas por los contratistas de concreto. La abrazadera llegó a ser rápidamente popular y los contratistas pidieron que él hiciera más equipo para resolver sus necesidades en la construcción de concreto. Pronto, A.H. Symons hacía una variedad amplia de equipo para la cada vez mayor industria de la construcción en concreto.
·1902
August Perret diseñó y construyó un edificio de apartamentos en París que usa las aplicaciones qué él llamó "sistema trabeated para el concreto reforzado". Fue estudiado y también imitado ampliamente y además influenció profundamente la construcción en concreto por décadas.
August Perret diseñó los apartamentos en la 25bis el rue Franklin con vistas maravillosas hacia el Río Sena y la Torre Eiffel. Su área agrandada de ventanas con las pequeñas masas de soporte fue radical en sus días. Se considera una estructura seminal en el temprano movimiento arquitectónico moderno porque utilizó la fuerza extraordinaria del concreto reforzado para crear un edificio que tenía un marco de soporte que no dependía del espesor de las paredes.
Templo Unity
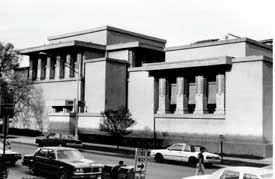
Frank Lloyd Wright comenzó la construcción del famoso templo de la Unidad en Oak Park, Illinois. Tomando tres años para terminar, Wright diseñó la masiva estructura con cuatro caras idénticas de modo que su costoso encofrado se pudiera utilizar múltiples veces.
Falling Waters
Frank Lloyd Wright creyó que el concreto era un material de construcción importante que debe ser utilizado en muchas maneras. Él lo utilizó como vigas ocultas de ayuda, losas, paredes y techos en la mayoría de sus trabajos desde 1903 en adelante.
El templo de la unidad se hizo casi enteramente de concreto reforzado; la famosa casa "Falling Waters" usa las losas de concreto para soporte y efecto dramático; en muchos de sus trabajos posteriores usó sus bloques de concreto diseñados para soporte y efecto decorativo.
·1908 - Edison con casa modelo
Thomas Edison creyó que el concreto era el material que revolucionaría los hogares. Él quería que el trabajador promedio pudiera vivir en casas finas, que el concreto haría rentable. Este modelo adornado era similar a los 11 hogares que él construyó. Usando concreto y formas avanzados, cada hogar era vertido de piso a techo en un día.
·1914 - La construcción del Canal de Panamá
El Canal de Panamá fue abierto después de décadas de construcción. Ofrece tres pares de exclusas de concreto con suelos tan gruesos como 20 pies y las paredes tan gruesas como 60 pies en el fondo.
El Canal de Panamá tomó más de 30 años para terminarse a un costo de $347 millones. Los desafíos de ingeniería encontrados fueron enormes. Las condiciones geológicas difíciles, la obtención de las materias primas necesarias y mano de obra, más la enorme escala del equipo requirieron la innovación ilimitada. Las formas de acero para las superficies interiores de las exclusas fueron 80 pies de alto y 36 pies de ancho.
·1917 - El local en Chicago
Symons se mudó a un local más grande en Chicago para acomodar el crecimiento.
Arthur Henry Symons mudó su negocio desde la ciudad de Kansas a Chicago en 1917 para acomodar el crecimiento del negocio. El estar más cerca al buen transporte para la adquisición de la materia prima y distribución del producto, trabajo experto y un mercado que crecía estimuló más crecimiento.
·1918 - Anuncio
Symons lanzó su primer anuncio en la Engineering News-Review (ENR). Esto extendió la palabra sobre sus productos y dió lugar incluso a mayor crecimiento y expansión de los productos y servicios de Symons.
"La abrazadera de columna SYMONS" dice el título en el primer anuncio de Symons en la Engineering News-Review (ENR). Este anuncio apareció en la edición de ENR del 14 agosto de 1918 y se han estado publicando anuncios allí desde entonces.
·1921 - Hangar de aeronaves
Los vastos y parabólicos hangares de dirigibles en el aeropuerto de Orly en París fueron terminados.
Los hangares extensos de los dirigibles de Eugene Freyssinet (comenzados en 1916) fueron construidos de costillas parabólicas pretensadas. La forma permitió la más grande y posible fuerza estructural para el enorme volumen necesario para contener los dirigibles. La naturaleza incombustible del concreto fue el factor principal que convenció al equipo de Orly a que aprobara el diseño altamente inusual.
·1933 - Alcatraz
La Penitenciaría de Alcatraz fue abierta. Los primeros internos fueron la cuadrilla de trabajo de la prisión que la construyó.
Esta prisión federal en la isla de Alcatraz fue cerrada por el ejército en 1933 y se convirtió oficialmente en una Penitenciaría en 1934. El agregado para el concreto en muchos de los edificios es ladrillo machacado de la prisión militar.
·1946 - Wood-Ply®
·1955 - Steel-Ply®
El sistema de Steel-Ply combina los resistentes carrioles de acero y los travesaños con el chapeado especial de Symons de ½" de plywood HDO para un grado de 1000 psf. Este grado de la carga:
· Reduce los requisitos de unión comparados al encofrado típico trabajo-construído.
· Aumenta la productividad
·1973 - La Casa de Ópera
Se inaugura la casa de ópera en Sydney, Australia. Sus distintivos picos de concreto se convirtieron rápidamente en un símbolo para la ciudad.
La distribución internacional de los productos de Symons comienza.
La línea dramática de la azotea en la Casa de Ópera en Sydney es una perdurable imagen de Sydney, Australia. Las múltiples áreas de presentaciones dentro de los picos son reconocidas por sus exquisitas calidades acústicas.
·1982
La línea química de productos de concreto de Symons de amplía con la introducción de desbloqueadores líquidos, compuestos para curar, selladores de acrílico y endurecedores.
·1987 - Room Tunnel
Se introducen el "Room Tunnel" molde para el formado repetitivo de cuartos y el sistema de formación de concreto "Flex-Form" para paredes curvas.
El sistema de formado Room Tunnel es un sistema de "medio túnel" que es más simple, más ligero y más rápido de manejar que productos competidores de "túnel entero". El diseño del "medio túnel" también proporciona una mayor flexibilidad dimensional para la potencial reutilización en otros proyectos.
El "Room Tunnel" está diseñado con un revestimiento de placa 3/16" de acero respaldada con costillas de acero. Este robusto diseño reduce al mínimo el apoyo interior para lograr un área despejada. El diseño también proporciona un acabado liso sin desviación. Los asentamientos magnéticos rápidos y eficientes reducen los costos para los bordes y los "blockouts" de la losa, mejorando la duración del ciclo.
El sistema "Room Tunnel" se ha utilizado para "un cuarto, por día, por forma". Eso significa horarios más rápidos para la terminación del proyecto y costos reducidos para el contratista y el propietario.
Los paneles de "Flex-Form" se entregan al sitio del trabajo pre-ensamblados al radio requerido. No hay costosos modelos trabajo-construidos necesarios para poner este sistema patentado de formación en uso.
El sistema de "Flex-Form" consiste en un panel flexible 3/16" de acero que sigue la forma de una costilla rodada en ángulo. La costilla se emperna a los refuerzos del panel para llevar a cabo con seguridad la forma al radio especificado. Cambiar el radio de formación para diversas condiciones del proyecto es tan simple como cambiar la costilla.
El sistema de formación de concreto "Flex-Form" produce una excelente superficie de concreto que no requiere normalmente ningún acabado adicional. Debido a que el panel de "Flex-Form" se dobla para formar el radio, las estrías se eliminan virtualmente.
·1993 - Museo JFK
El Museo John F. Kennedy en Boston fue terminado. La dramática estructura de concreto y cristal fue diseñada por el reconocido arquitecto I. M. Pei.
La ceremonia de dedicatoria para el Museo John Fitzgerald Kennedy fue presidida por el presidente Clinton. Él comentó de su reunión en su infancia con el presidente Kennedy y cómo éste influenció su vida.
El museo por sí mismo es una estructura dramáticamente angular de cristal verde y concreto blanco que se aprovecha del inclinado terreno costero con dramáticas vistas del mar y de la ciudad.
·1996
La manija de "Quick-Hook" es una parte integral de cada panel de "Steel-Ply" y de varias tallas del llenador. Provee a los trabajadores las puntas de conexión convenientes para el harness de seguridad al subir y trabajar con el "Steel-Ply" que forma el sistema.
Cuando los paneles de "Steel-Ply" con la manija "Quick-Hook" se utilizan en una aplicación gangforming, las manijas nunca están más de 3 pies separadas. Un trabajador puede moverse fácilmente arriba, abajo y a través de la cuadrilla alternativamente enganchando y soltando los ganchos de seguridad asociados al equipo de protección de caídas.
Ingredientes del concreto en la actualidad



El concreto fresco es una mezcla semilíquida de cemento portland, arena (agregado fino), grava o piedra triturada (agregado grueso) yagua. Mediante un proceso llamado hidratación, las partículas del cemento reaccionan químicamente con el agua y el concreto se endurece y se convierte en un material durable. Cuando se mezcla, se hace el vaciado y se cura de manera apropiada, el concreto forma estructuras sólidas capaces de soportar las temperaturas extremas del invierno y del verano sin requerir de mucho mantenimiento. El material que se utilice en la preparación del concreto afecta la facilidad con que pueda vaciarse y con la que se le pueda dar el acabado; también influye en el tiempo que tarde en endurecer, la resistencia que pueda adquirir, y lo bien que cumpla las funciones para las que fue preparado.
Además de los ingredientes de la mezcla de concreto en sí misma, será necesario un marco o cimbra y un refuerzo de acero para construir estructuras sólidas. La cimbra generalmente se construye de madera y puede hacerse con ella desde un sencillo cuadrado hasta formas más complejas, dependiendo de la naturaleza del proyecto. El acero reforzado puede ser de alta o baja resistencia, características que dependerán de las dimensiones y la resistencia que se requieran. El concreto se vacía en la cimbra con la forma deseada y después la superficie se alisa y se le da el acabado con diversas texturas.
Concreto recién mezclado
El concreto recién mezclado debe ser plástico o semifluido y capaz de ser moldeado a mano. Una mezcla muy húmeda de concreto se puede moldear en el sentido de que puede colocarse en una cimbra, pero esto no entra en la definición de " plástico " aquel material que es plegable y capaz de ser moldeado o formado como un terrón de arcilla para moldar.
En una mezcla de concreto plástico todos los granos de arena y las piezas de grava o de piedra que eran encajonados y sostenidos en suspensión. Los ingredientes no están predispuestos a segregarse durante el transporte; y cuando el concreto endurece, se transforma en una mezcla homogénea de todos los componentes. El concreto de consistencia plástica no se desmorona si no que fluye como liquido viscoso sin segregarse.
El revenimiento se utiliza como una medida de la consistencia del concreto. Un concreto de bajo revenimiento tiene una consistencia dura. En la practica de la construcción, los elementos delgados de concreto y los elementos del concreto fuertemente reforzados requieren de mezclas trabajables, pero jamás de mezclas similares a una sopa, para tener facilidad en su colocación. Se necesita una mezcla plástica para tener resistencia y para mantener su homogeneidad durante el manejo y la colocación. Mientras que una mezcla plástica es adecuada para la mayoría con trabajos con concreto, se puede utilizar aditivos superfluidificantes para adicionar fluidez al concreto en miembros de concretos delgados o fuertemente reforzados.
Mezclado
Los 5 componentes básicos del concreto deben ser combinados en una mezcla homogénea que requiere esfuerzo y cuidado. La secuencia de carga de los ingredientes en la mezcladora representa un papel importante en la uniformidad del producto terminado. Sin embargo, se puede variar esa secuencia y aun así producir concreto de calidad. Las diferentes secuencias requieren ajustes en el tiempo de adicionamiento de agua, en el número total de revoluciones del tambor de la mezcladora, y en la velocidad de revolución.
Otros factores importantes en el mezclado son el tamaño de la revoltura en la relación al tamaño del tambor de la mezcladora, el tiempo transcurrido entre la dosificación y el mezclado, el diseño, la configuración y el estado del tambor mezclador y las paletas. Las mezcladoras aprobadas, con operación y mantenimiento correcto, aseguran un intercambio de materiales de extremo a extremo por medio de una acción de rolado, plegado y amasado de la revoltura sobre si misma a medida que se mezcla el concreto.
Trabajabilidad
La facilidad de colocar, consolidar y acabar al concreto recién mezclado. se denomina trabajabilidad.
El concreto debe ser trabajable pero no se debe segregar excesivamente. El sangrado es la migración de el agua hacia la superficie superior del concreto recién mezclado provocada por el asentamiento de los materiales Sólidos – Cemento, arena y piedra dentro de la masa. El asentamiento es consecuencia del efecto combinado del la vibración y de la gravedad.
Un sangrado excesivo aumenta la relación Agua - Cemento cerca de la superficie superior, pudiendo dar como resultado una capa superior débil de baja durabilidad, particularmente si se lleva acabo las operaciones de acabado mientras esta presente el agua de sangrado. Debido a la tendencia del concreto recién mezclado a segregarse y sangrar, es importante transportar y colocar cada carga lo mas cerca posible de su posición final. El aire incluido mejor a la trabajabilidad y reduce la tendencia del concreto fresco de segregarse y sangrar.
Consolidación
La vibración pone en movimiento a las partículas en el concreto recién mezclado, reduciendo la fricción entre ellas y dándole a la mezcla las cualidades movilies de un fluido denso. La acción vibratoria permite el uso de la mezcla dura que contenga una mayor proporción de agregado grueso y una menor proporción de agregado fino. Empleando un agregado bien graduado, entre mayor sea el tamaño máximo del agregado en el concreto, habrá que llenar pasta un menor volumen y existirá una menor área superficial de agregado por cubrir con pasta, teniendo como consecuencia que una cantidad menor de agua y de cemento es necesaria. con una consolidación adecuada de las mezclas mas duras y ásperas pueden ser empleadas, lo que tiene como resultado una mayor calidad y economía.
Si una mezcla de concreto es lo suficientemente trabajable para ser consolidada de manera adecuada por varillado manual, puede que no exista ninguna ventaja en vibrarla. De hecho, tales mezclas se pueden segregar al vibrarlas. Solo al emplear mezclas mas duras y ásperas se adquieren todos los beneficios de l vibrado.
El vibrado mecánico tiene muchas ventajas. Los vibradores de alta frecuencia posibilitan la colocación económica de mezclas que no son facilites de consolidar a mano bajo ciertas condiciones.
La propiedad de liga de las pastas de cemento Portland se debe a la reaccion química entre el cemento y el agua llamada hidratación.
El cemento Portland no es un compuesto químico simple, sino que es una mezcla de muchos compuestos. Cuatro de ellos conforman el 90% o mas de el peso del cemento Portland y son: el silicato tricalcico, el silicato dicalcico, el aluminiato tricalcico y el aluminio ferrito tetracalcico. Ademas de estos componentes principales, algunos otros desempeñan papeles importantes en el proceso de hidratación. Los tipos de cemento Portland contienen los mismos cuatro compuestos principales, pero en proporciones diferentes.
Cuando el Clinker (el producto del horno que se muele para fabricar el cemento Portland) se examina al microscopio, la mayoría de los compuestos individuales del cemento se pueden identificar y se puede determinar sus cantidades. Sin embargo, los granos mas pequeños evaden la detección visual. El diámetro promedio de una particula de cemento tipica es de aproximadamente 10 micras, o una centésima de milímetro. Si todas las partículas de cemento fueran las promedio, el cemento Portland contendría aproximadamente 298,000 millones de granos por kilogramo, pero de hecho existen unos 15 billones de partículas debido al alto ronago de tamaños de particula. Las particulas en un kilogramo de cemento Portland tiene una area superficial aproximada de 400 metros cuadrados.
Los dos silicatos de calcio, los cuales constituyen cerca del 75% del peso del cemento Portland, reaccionan con el agua para formar dos nuevos compuestos: el hidróxido de calcio y el hidrato de silicato de calcio. Este ultimo es con mucho el componente cementante mas importante en el concreto. Las propiedades ingenieriles del concreto, - fraguado y endurecimiento, resistencia y estabilidad dimensional - principalmente depende del gel del hidrato de silicato de calcio. Es la medula del concreto.
La composición química del silicato de calcio hidratado es en cierto modo variable, pero contiene cal (CaO) y silice (Si02), en una proporción sobre el orden de 3 a 2. el area superficial del hidrato de silicato de calcio es de unos 3000 metros cuadrados por gramo. Las particulas son tan diminutas que solamente ser vistas en microscopio electrónico. En la pasta de cemento ya endurecida, estas partículas forman uniones enlazadas entre las otras fases cristalinas y los granos sobrantes de cemento sin hidratar; tambien se adhieren a los granos de arena y a piezas de agregado grueso, cementando todo el conjunto. La formación de esta estructura es la accion cementante de la pasta y es responsable del fraguado, del endurecimiento y del desarrollo de resistencia.
Cuando el concreto fragua, su volumen bruto permanece casi inalterado, pero el concreto endurecido contiene poros llenos de agua y aire, mismos que no tienen resistencia alguna. La resistencia esta en la parte solida de la pasta, en su mayoría en el hidrato de silicato de calcio y en las faces cristalinas.
Entre menos porosa sea la pasta de cemento, mucho mas resistente es el concreto. Por lo tanto, cuando se mezcle el concreto no se debe usar una cantidad mayor de agua que la absolutamente necesaria para fabricar un concreto plástico y trabajable. A un entonces, el agua empleada es usualmente mayor que la que se requiere para la completa hidratación del cemento. La relación mínima Agua – Cemento (en peso) para la hidratación total es aproximadamente de 0.22 a 0.25.
El conocimiento de la cantidad de calor liberan do a medida de que el cemento se hidrato puede ser util para planear la construcción. En invierno, el calor de hidratación ayudara a proteger el concreto contra el daño probocado por temperaturas de congelecion. Sin embargo, el calor puede ser en estructuras masivas, tales como presas, porque puede producir esfuerzos indeseables al enfriarse luego de endurecer. El cemento Portland tipo 1 un poco mas de la mitad de su calor total de hidratación en tres días. El cemento tipo 3, de alta resistencia temprana, libera aproximadamente el mismo procentaje de su calor en mucho menos de tres dias. El cemento tipo 2, un cemento de calor moderado, libera menos calor total que los otros y deben pasar mas de tres dias para que se libere unicamente la mitad de ese calor. El uso de cemento tipo 4, cemente Portland de bajo calor de hidratación, se debe de tomar en cosideracion donde sea de importancia fundamental contar con un bajo calor de hidratación.
Es importante conocer la velocidad de reacción entre el cemento y el agua porque la velocidad de terminada el tiempo de fraguado y de endurecimiento. La reacción inicial debe ser suficientemente lenta para que conseda tiempo al transporte y colocasion del concreto. Sin embargo, una vez que el concreto ha sido colocado y terminado, es deseable tener un endurecimiento rapido. El yeso, que es adicionado en el molino de cemento durante la molienda del Clinker, actua como regulador de la velocidad inicial de hidratación del cemento Portland. Otros factores que influyen en la velocidad de hidratación incluyen la finura de molienda, los aditivos, la cantidad de agua adicionada y la temperatura de los materiales en el momento del mezclado.
Concreto endurecido curado humedo
Si se vuelve a saturar el concreto luego de un periodo de secado, la hidratación se reanuda y la resistencia vuelve a aumentar. Sin embargo lo mejor es aplicar el curado húmedo al concreto de manera continua desde el momento en que se ha colocado hasta cuando haya alcanzado la calidad deseada debido a que el concreto es difícil de resaturar.
Velocidad de secado del concreto
El cocreto ni endurece ni se cura con el secado. El concreto (o de manera precisa, el cemento en el contenido) requiere de humedad para hidratarse y endurecer. El secado del concreto unicamente esta relacionado con la hidratación y el endurecimiente de manera indirecta. Al secarse el concreto, deja de ganar resistencia; el hecho de que este seco, no es indicación de que haya experimentado la suficiente hidratación para lograr las propiedades fisicas deseadas.
El conocimiento de la velocidad de secado es útil para comprender las propiedades o la condición física del concreto. Por ejemplo, tal como se menciono, el concreto debe seguir reteniendo suficiente humedad durante todo el perido de curado para que el cemento pueda hidratarse. El concreto recién colado tiene agua abundante, pero a medida de que el secado progresa desde la superficie hacia el interior, el aumento de resistencia continuara a cada profundidad únicamente mientras la humedad relativa en ese punto se mantenga por encima del 80%.
La superficie de un piso de concreto que no a tenido suficiente curado húmedo es una muestra común. Debido a que se seca rápidamente, el concreto de la superficie es débil y se produce descascaramiento en partículas finas provocado por el transito. Asimismo, el concreto se contrae al, secarse, del mismo modo que lo hacen la madera, papel y la arcilla (aunque no tanto). La contraccion por secado es una causa fundamental de agrietamiento, y le ancho de las grietas es función del grado del secado.
En tanto que la superficie del concreto se seca rápidamente, al concreto en el interior le lleva mucho mas tiempo secarse.
Note que luego de 114 días de secado natural el concreto aun se encuentra muy húmedo en su interior y que se requiere de 850 días para que la humedad relativa en el concreto descendiera al 50%.
El contenido de humedad en elementos delgados de concreto que han sido secado al aire con una humedad relativa de 50% a 90% durante varios meses es de 1% a 2% en peso del concreto, del contenido original de agua, de las condiciones de secado y del tamaño del elemento de concreto.
El tamaño y la forma de un miembro de concreto mantiene una relación importante como la velocidad de secado. Los elementos del concreto de gra area superficial en relacion a su volumen (tales como losas de piso) se secan con mucho mayor rapidez que los grandes volumenes de concreto con ares superficiales relativamente pequeñas (tales como los estribos de puentes).
Muchas otras propiedades del concreto endurecido se ven también afectadas por su contenido de humedad; en ellas incluye la elasticidad, flujo plástico, valor de aislamiento, resistencia al fuego, resistencia al desgaste, conductividad eléctrica, durabilidad.
Resistencia
La resistencia a la compresión se puede definir como la máxima resistencia medida de un espécimen de concreto o de mortero a carga axial. Generalmente se expresa en kilogramos por centímetro cuadrado (Kg/cm2) a una edad de 28 días se le designe con el símbolo f’ c. Para de terminar la resistencia a la compresión, se realizan pruebas especimenes de mortero o de concreto; en los Estados Unidos, a menos de que se especifique de otra manera, los ensayes a compresión de mortero se realizan sobre cubos de 5 cm. en tanto que los ensayes a compresión del concreto se efectúan sobre cilindros que miden 15 cm de diámetro y 30 cm de altura.
La resistencia del concreto a la compresión es una propiedad física fundamental, y es frecuentemente empleada el los cálculos para diseño de puente, de edificios y otras estructuras. El concreto de uso generalizado tiene una resistencia a la compresión entre 210 y 350 kg/cm cuadrado. un concreto de alta resistencia tiene una resistencia a la compresión de cuando menos 420 kg/cm cuadrado. resistencia de 1,400 kg/cm cuadrado se ha llegado a utilizar en aplicaciones de construcción .
La resistencia a la flexión del concreto se utiliza generalmente al diseñar pavimentos y otras losas sobre el terreno. La resistencia a la compresión se puede utilizar como índice de la resistencia a la flexión, una ves que entre ellas se ha establecido la relación empírica para los materiales y el tamaño del elemento en cuestión. La resistencia a la flexión, también llamada modulo de ruptura, para un concreto de peso normal se aproxima a menudo de1.99 a 2.65 veces el valor de la raíz cuadrada de la resistencia a la compresión.
El valor de la resistencia a la tensión del concreto es aproximadamente de 8% a 12% de su resistencia a compresión y a menudo se estima como 1.33 a 1.99 veces la raíz cuadrada de la resistencia a compresión.
La resistencia a la torsión para el concreto esta relacionada con el modulo de ruptura y con las dimensiones del elemento de concreto.
La resistencia al cortante del concreto puede variar desde el 35% al 80% de la resistencia a compresión. La correlación existe entre la resistencia a la compresión y resistencia a flexión, tensión, torsión, y cortante, de acuerdo a los componentes del concreto y al medio ambiente en que se encuentre.
El modulo de elasticidad, denotando por medio del símbolo E, se puedes definir como la relación del esfuerzo normal la deformación correspondiente para esfuerzos de tensión o de compresión por debajo del limite de proporcionalidad de un material. Para concretos de peso normal, E fluctúa entre 140,600 y 422,000 kg/cm cuadrado, y se puede aproximar como 15,100 veces el valor de la raíz cuadrada de la resistencia a compresión.
Los principales factores que afectan a la resistencia son la relación Agua – Cemento y la edad, o el grado a que haya progresado la hidratación. Estos factores también afectan a la resistencia a flexión y a tensión, así como a la adherencia del concreto con el acero.
Las relaciones Edad – Resistencia a compresión. Cuando se requiera de valores mas precisos para el concreto se deberán desarrollar curvas para los materiales específicos y para las proporciones de mezclado que se utilicen en el trabajo.
Para una trabajabilidad y una cantidad de cemento dadas, el concreto con aire incluido necesita menos agua de mezclado que el concreto sin aire incluido. La menor relación Agua – Cemento que es posible lograr en un concreto con aire incluido tiende a compensar las resistencias mínimas inferiores del concreto con aire incluido, particularmente en mezclas con contenidos de cemento pobres e intermedios.
Peso unitario
El concreto convencional, empleado normalmente en pavimentos, edificios y en otras estructuras tiene un peso unitario dentro del rango de 2,240 y 2,400 kg por metro cúbico (kg/m3). El peso unitario (densidad) del concreto varia, dependiendo de la cantidad y de la densidad relativa del agregado, de la cantidad del aire atrapado o intencionalmente incluido, y de los contenidos de agua y de cemento, mismos que a su vez se ven influenciados por el tamaño máximo del agregado. Para el diseño de estructuras de concreto, comúnmente se supone que la combinación del concreto convencional y de las barras de refuerzo pesa 2400 kg/m3.
El peso del concreto seco iguala al peso del concreto recién mezclado menos el peso del agua evaporable. Una parte del agua de mezclado se combina químicamente con el cemento durante el proceso de hidratación, transformando al cemento en gel de cemento. También un poco de agua permanece retenida herméticamente en poros y capilares y no se evapora bajo condiciones normales. La cantidad de agua que se evapora al aire a una humedad relativa del 50% es de aproximadamente 2% a 3% del peso del concreto, dependiendo del contenido inicial de agua del concreto, de las características de absorción de los agregados, y del tamaño de la estructura.
Además del concreto convencional, existe una amplia variedad de otros concretos para hacer frente a diversas necesidades, variando desde concretos aisladores ligeros con pesos unitarios de 240 kg/m3, a concretos pesados con pesos unitarios de 6400 kg/m3, que se emplean para contrapesos o para blindajes contra radiaciones.
Resistencia a congelación y deshielo
Del concreto utilizado en estructuras y pavimentos, se espera que tenga una vida larga y un mantenimiento bajo. Debe tener buena durabilidad para resistir condiciones de exposición anticipadas. El factor de intemperismo mas destructivo es la congelación y el deshielo mientras el concreto se encuentra húmedo, particularmente cuando se encuentra con la presencia de agentes químicos descongelantes. El deterioro provocado por el congelamiento del agua en la pasta, en las partículas del agregado o en ambos.
Con la inclusión de aire es sumamente resistente a este deterioro. Durante el congelamiento, el agua se desplaza por la formación de hielo en la pasta se acomoda de tal forma que no resulta perjudicial; las burbujas de aire en la pasta suministran cámaras donde se introduce el agua y asi se alivia la presión hidráulica generada.
Cuando la congelación ocurre en un concreto que contenga agregado saturado, se pueden generar presiones hidráulicas nocivas dentro del agregado. El agua desplazada desde las partículas del agregado durante la formación del hielo no puede escapar lo suficientemente rápido hacia la pasta circundante para aliviar la presión. Sin embargo, bajo casi todas las condiciones de exposición, una pasta de buena calidad (de baja relación Agua – Cemento) evitara que la mayor parte de las partículas de agregado se saturen. También, si la pasta tiene aire incluido, acomodara las pequeñas cantidades de agua en exceso que pudieran ser expulsadas por los agregados, protegiendo así al concreto contra daños por congelación y deshielo.
(1): El concreto con aire incluido es mucho mas resistente a los ciclos de congelación y deshielo que el concreto sin aire incluido, (2): el concreto con una relación Agua – Cemento baja es mas durable que el concreto con una relación Agua – Cemento alta, (3) un periodo de secado antes de la exposición a la congelación y el deshielo beneficia sustancialmente la resistencia a la congelación y deshielo beneficia sustancialmente la resistencia a la congelación y el deshielo del concreto con aire incluido , pero no beneficia de manera significativa al concreto sin aire incluido. El concreto con aire incluido con una relación Agua – Cemento baja y con un contenido de aire de 4% a 8% soportara un gran numero de ciclos de congelación y deshielo sin presentar fallas.
Permeabilidad y hermeticidad
El concreto empleado en estructuras que retengan agua o que esten expuestas a mal tiempo o a otras condiciones de exposición severa debe ser virtualmente impermeable y hermético. La hermeticidad se define a menudo como la capacidad del concreto de refrenar o retener el agua sin escapes visibles. La permeabilidad se refiere a la cantidad de migración de agua a través del concreto cuando el agua se encuentra a presión, o a la capacidad del concreto de resistir la penetración de agua u atrás sustancias (liquido, gas, iones, etc.). Generalmente las mismas propiedades que covierten al concreto menos permeable también lo vuelven mas hermético.
La permeabilidad total del concreto al agua es una función de la permeabilidad de la pasta, de la permeabilidad y granulometria del agregado, y de la proporción relativa de la pasta con respecto al agregado. la disminución de permeabilidad mejora la resistencia del concreto a la resaturacion, a l ataque de sulfatos y otros productos químicos y a la penetración del ion cloruro.
La permeabilidad también afecta la capacidad de destrucción por congelamiento en condiciones de saturación. Aquí la permeabilidad de la pasta es de particular importancia porque la pasta recubre a todos los constituyentes del concreto. La permeabilidad de la pasta depende de la relación Agua – Cemento y del agregado de hidratación del cemento o duracion del curado húmedo. Un concreto de baja permeabilidad requiere de una relación Agua – Cemento baja y un periodo de curado húmedo adecuado. Inclusion de aire ayuda a la hermeticidad aunque tiene un efecto mínimo sobre la permeabilidad aumenta con el secado.
La permeabilidad de una pasta endurecida madura mantuvo continuamente rangos de humedad de 0.1x10E- 12cm por seg. para relaciones Agua – Cemento que variaban de 0.3 a 0.7. La permeabilidad de rocas comúnmente utilizadas como agregado para concreto varia desde aproximadamente 1.7 x10E9 hasta 3.5x10E-13 cm por seg. La permeabilidad de un concreto maduro de buena calidad es de aproximadamente 1x10E- 10cm por seg.
Los resultados de ensayes obtenidos al sujetar el discos de mortero sin aire incluido de 2.5cm de espesor a una presión de agua de 1.4 kg/cm cuadrado. En estos ensayes, no existieron fugas de agua a través del disco de mortero que tenia relación Agua – Cemento en peso iguales a 0.50 o menores y que hubieran tenido un curado húmedo de siete días. Cuando ocurrieron fugas, estas fueron mayores en los discos de mortero hechos con altas relaciones Agua – Cemento. También, para cada relación Agua – Cemento, las fugas fueron menores a medida que se aumentaba el periodo de curado húmedo. En los discos con una relación agua cemento de 0.80 el mortero permitía fugas a pesar de haber sido curado durante un mes. Estos resultados ilustran claramente que una relación Agua - cemento baja y un periodo de curado reducen permeabilidad de manera significativa.
Las relaciones Agua – Cemento bajas también reducen la segregación y el sangrado, contribuyendo adicionalmente a la hermeticidad. Para ser hermético, el concreto también debe estar libre de agrietamientos y de celdillas.
Ocasionalmente el concreto poroso – concreto sin finos que permite fácilmente el flujo de agua a traves de si mismo – se diseña para aplicaciones especiales. En estos concretos, el agregado fino se reduce grandemente o incluso se remueve totalmente produciendo un gran volumen de huecos de aire. El concreto poroso ha sido utilizado en canchas de tenis, pavimentos, lotes para estacionamientos, invernaderos estructuras de drenaje. El concreto excluido de finos también se ha empleado en edificios a sus propiedades de aislamiento térmico.
Los pisos, pavimentos y estructuras hidráulicas están sujetos al desgaste; por tanto, en estas aplicaciones el concreto debe tener una resistencia elevada a la abrasion. Los resultados de pruebas indican que la resistencia a la abrasion o desgaste esta estrechamente relacionada con la resistencia la compresión del concreto. Un concreto de alta resistencia a compresión tiene mayor resistencia a la abrasión que un concreto de resistencia a compresión baja. Como la resistencia a la compresión depende de la relación Agua – Cemento baja, así como un curado adecuado son necesarios para obtener una buena resistencia al desgaste. El tipo de agregado y el acabado de la superficie o el tratamiento utilizado también tienen fuerte influencia en la resistencia al desgaste. Un agregado duro es más resistente a la abrasión que un agregado blando y esponjoso, y una superficie que ha sido tratada con llana de metal resistente mas el desgaste que una que no lo ha sido.
Estabilidad y Volumétrica
El concreto endurecido presenta ligeros cambios de volumen debido a variaciones en la temperatura, en la humedad en los esfuerzos aplicados. Estos cambios de volumen o de longitud pueden variar de aproximadamente 0.01% hasta 0.08%. En le concreto endurecido los cambios de volumen por temperatura son casi para el acero.
El concreto que se mantiene continuamente húmedo se dilatara ligeramente. Cuando se permite que seque, el concreto se contrae. El principal factor que influye en la magnitud de la contracción por el secado aumenta directamente con los incrementos de este contenido de agua. La magnitud de la contracción también depende de otros factores, como las cantidades de agregado empleado, las propiedades del agregado, tamaño y forma de la masa de concreto, temperatura y humedad relativa del medio ambiente, método de curado, grado de hidratación, y tiempo. El contenido de cemento tiene un efecto mínimo a nulo sobre la contracción por secado para contenidos de cemento entre 280 y 450 kg por metro cúbico.
Cuando el concreto se somete a esfuerzo, se forma elásticamente. Los esfuerzos sostenidos resultan en una deformación adicional llamada fluencia. La velocidad de la fluencia (deformación por unidad de tiempo ) disminuye con el tiempo.
Control de agretiamiento
Las dos causas básicas por las que se producen grietas en el concreto son (1) esfuerzos debidos a cargas aplicadas y (2) esfuerzos debidos a contracción por secado o a cambios de temperatura en condiciones de restricción
La contracción por secado es una propiedad inherente e inevitable del concreto, por lo que se utiliza acero de refuerzo colocado en una posición adecuada para reducir los anchos de grieta, o bien juntas que predetermine y controlen la ubicación de las grietas. Los esfuerzos provocados por las fluctuaciones de temperatura pueden causar agrietamientos, especialmente en edades tempranas.
Las grietas por contracción del concreto ocurren debido a restricciones. Si no existe una causa que impida el movimiento del concreto y ocurren contracciones, el concreto no se agrieta. Las restricciones pueden ser provocadas por causas diversas. La contracción por de secado siempre es mayor cerca de la superficie del concreto; las porciones húmedas interiores restringen al concreto en las cercanías de la superficie con lo que se pueden producir agrietamientos. Otras causas de restricción son el acero de refuerzo embebido e el concreto, las partes de una estructura interconectadas entre si, y la fricción de la subrasante sobre la cual va colocado el concreto.
Las juntas son el método mas efectivo para controlar agrietamientos. Si una extensión considerable de concreto (una pared, losa o pavimento) no contiene juntas convenientemente espaciadas que alivien la contracción por secado y por temperatura, el concreto se agrietara de manera aleatoria.
Las juntas de control se ranuran, se Forman o se aserran en banquetas, calzadas, pavimentos, pisos y muros de modo que las grietas ocurran en esas juntas y no aleatoriamente. Las juntas de control permiten movimientos en el plano de una losa o de un muro. Se desarrollan aproximadamente a un cuarto del espesor del concreto.
Las juntas de separación aíslan a una losa de otros elementos e otra estructura y le permiten tanto movimiento horizontales como verticales. Se colocan en las uniones de pisos con muros, columnas, bases y otros puntos donde pudieran ocurrir restricciones. Se desarrollan en todo el espesor de la losa e incluyen un relleno premoldeado para la junta.
Las juntas de construcción se colocan en los lugares donde ha concluido la jornada de trabajo; separan áreas de concreto colocado en distintos momentos. En las losas para pavimentos, las juntas de construcción comúnmente se alinean con las juntas de control o de separación, y funcionan también como estas últimas.
Agua de mezclado para el concreto
Casi cualquier agua natural que sea potable y que no tenga sabor u olor pronunciado, se puede utilizar para producir concreto. Sin embargo, algunas aguas no potables pueden ser adecuadas para el concreto.
Se puede utilizar para fabricar concreto si los cubos de mortero (Norma ASTM C109 ), producidos con ella alcanzan resistencia alos siete días iguales a al menos el 90% de especímenes testigo fabricados con agua potable o destilada.
Las impurezas excesivas en el agua no solo pueden afectar el tiempo de fraguado y la resistencia de el concreto, si no también pueden ser causa de eflorescencia, manchado, corrosion del esfuerzo, inestabilidad volumétrica y una menor durabilidad.
El agua que contiene menos de 2,000 partes de millón (ppm) de sólidos disueltos totales generalmente pueden ser utilizada de manera satisfactoria para elaborar concreto. El agua que contenga mas de 2,000 ppm de sólidos disueltos debera ser ensayada para investigar su efecto sobre la resistencia y el tiempo de fraguado.
Carbonatos y Bicarbonatos alcalinos
El carbonato de sodio puede causar fraguados muy rápidos, en tanto que lo bicarbonatos pueden acelerar o retardar el fraguado. En concentraciones fuertes estas sales pueden reducir de manera significativa la resistencia del concreto. Cuando la suma de las sales disueltas exceda 1,000 ppm, se deberan realizar pruebas para analizar su efecto sobre el tiempo de fraguado y sobre la resistencia a los 28 días. También se debera considerar la posibilidad que se presenten reacciones alcali – agregado graves.
Cloruros
La inquietud respecto a un elevado contenido de cloruros en el agua de mezclado, se debe principalmente al posible efecto adverso que lo iones de cloruro pudieran tener en la corrosion del acero de refuerzo, o de los torones del presfuerzo. Los iones cloruro atacan la capa de oxido protectora formada en el acero por el medio químico altamente alcalino (pH 12.5) presente en el concreto.
Los cloruros se pueden introdicir en el concreto, ya sea con los ingredientes separados – aditivos, agregados, cemento, y agua – o atraves de la exposición a las sales anticongelantes, al agua de mar, o al aire cargado de sales cerca de las costas.
El agua que se utilice en concreto preforzado o en un concreto que vaya a tener embebido aluminio no debera contener cantidades nocivas de ion cloruro. Las aportaciones de cloruros de los ingredientes distintos al agua también se deberán tomar en consideración. Los aditivos de cloruro de calcio se deberán emplear con mucha precaución.
El Reglamento de Construcción del American Concrete Institute, ACI 318, limita el contenido de ion cloruro soluble al agua en el concreto, a los siguientes porcentajes en peso del cemento.
Concreto preforzado.
Concreto reforzado expuesto a cloruros durante su servicio.
Concreto reforzado que vaya a estar seco o protegido contra la humedad durante su servicio.
Otras construcciones de concreto reforzado.
Sulfatos
Otras sales comunes
Los carbonatos de calcio y de magnesio no son muy solubles en el agua y rara ves se les encuentra en concentraciones suficientes para afectar la resistencia del concreto. En algunas aguas municipales se pueden encontrar bicarbonatos de calcio y de magnesio. No se consideran dañinas las concentraciones inferiores o iguales a 400 ppm de bicarbonato en estas formas.
Se han obtenido buenas resistencias con concentraciones hasta de 40,000 ppm de cloruro de magnesio. Las concentraciones e sulfato de magnesio deberán ser inferiores a 25,000 ppm.
Sales de hierro
Las aguas freaticas naturales rara vez contienen mas de 20 a30 ppm de hierro; sin embargo, las aguas de mina acidas pueden contener cantidades muy grandes. Las sales de hierro en concentraciones hasta 40,000 ppm normalmente no afectan de manera adversa al desarrollo de la resistencia.
Diversas sales inorgánicas
Las sales de magnesio, estaño, zinc, cobre y plomo presentes en el agua pueden provocar una reducción considerable en la resistencia y también grandes variaciones en el tiempo de fraguado. De estas, las mas activas son las sales de zinc, de cobre y de plomo. Las sales que son especialmente activas como retardantes, incluyen el yodato de sodio, fosfato de sodio, arsenato de sodio y borato de sodio.
Generalmente se pueden tolerar en el agua de mezclado concentraciones de estas sales hasta de 500 ppm.
Otra sal que puede ser dañina al concreto es el sulfuro de sodio; aun la presencia de 100 ppm requiere de ensayes.
Agua de mar
Aun cuando un concreto hecho con agua de mar puede tener una resistencia temprana mayor que un concreto normal, sus resistencias a edades mayores (después de 28 días) pueden ser inferiores. Esta reducción de resistencia puede ser compensada reduciendo la relación agua – cemento.
El agua de mar no es adecuada para producir concreto reforzado con acero y no debera usarse en concreto preforzados debido al riesgo de corrosion del esfuerzo, particularmente en ambientes cálidos y humedos.
El agua de mar que se utiliza para producir concreto, también tiende a causar eflorescencia y humedad en superficies de concreto expuestas al aire y al agua.
Aguas ácidas
En general, el agua de mezclado que contiene acidos clorhídrico, sulfúrico y otros acidos inorgánicos comunes en concentraciones inferiores a 10,000 ppm no tiene un efecto adverso en la resistencia. Las aguas acidas con valores pH menores que 3.0 pueden ocasionar problemas de manejo y se deben evitar en la medida de lo posible.
Aguas Alcalinas
Las aguas con concentraciones de hidróxido de sodio de 0.5% el peso del cemento, no afecta en gran medida a la resistencia del concreto toda vez que no ocasionen un fraguado rápido. Sin embargo, mayores concentraciones pueden reducir la resistencia del concreto.
El hidróxido de potasio en concentraciones menores a 1.2% por peso de cemento tiene poco efecto en la resistencia del concreto desarrollada por ciertos cementos, pero la misma concentracion al ser usada con otros cementos puede reducir sustancialmente la resistencia a los 28 días.
Aguas de enjuage
La Agencia de Protección Ambiental y las agencias estatales de los EEUU prohiben descargar en las vías fluviales, aguas de enjuague no tratadas que han sido utilizadas para aprovechar la arena y la grava de concretos regresados o para lavar las mezcladoras.
Aguas de desperdicios industriales
La mayor parte de las aguas que llevan desperdicios industriales tienen menos de 4,000 ppm de sólidos totales. Cuando se hace uso de esta agua como aguas de mezclado para el concreto, la reducción en la resistencia a la compresión generalmente no es mayor que del 10% al 15%.
Aguas negras
Las aguas negras típicas pueden tener aproximadamente 400 ppm de materia organica. Luego que esta aguas se han diluido en un buen sistema de tratamiento, la concentración se ve reducida aproximadamente 20 ppm o menos. Esta cantidad es demasiado pequeña para tener efecto de importancia en la resistencia.
Impurezas orgánicas
El efecto que las sustancias orgánicas presentes en las aguas naturales puedan tener en el tiempo de fraguado del cemento Portland o en la resistencia ultima del concreto, es un problema que presenta una complejidad considerable. Las aguas que esten muy coloreadas, las aguas con un olor notable o aquellas aguas en que sean visibles algas verdes o cafes deberán ser vistas con desconfianza y en consecuencia ensayadas.
Azúcar
Una pequeña cantidad de sacarosa, de 0.03% a 0.15% del peso del cemento, normalmente retarda el fraguado del cemento. El limite superior de este rango varia respecto de los distintos cementos. La resistencia a 7 dias puede verse reducida, en tanto que la resistencia a los 28 días podría aumentar. El azucar en cantidades de 0.25% o mas del peso del cemento puede provocar un fraguado rapido y una reducción sustancial de la resistencia a los 28 días. Cada tipo de azúcar afecta al tiempo de fraguado y a la resistencia de manera distinta.
Menos de 500 ppm de azucar en el agua de mezclado, generalmente no producen un efecto adverso en el desarrollo de la resistencia, pero si la concentración sobrepasa esta cantidad, se deberán realizar ensayes para analizar el tiempo de fraguado y el desarrollo de la resistencia.
Sedimientos o partículas en suspensión
Se puede tolerar en el agua aproximadamente 2,000 ppm de arcilla en suspension o de partículas finas de roca. Cantidades mayores podría no afectar la resistencia, pero bien podrían influir sobre otras propiedades de algunas mezclas de concreto. Antes ser empleada, cualquier agua lodosa debera pasar a través de estanques de sedimentación o deberá ser clarificada por cualquier otro medio para reducir la cantidad de sedimentos y de arcilla agregada a la mezcla. Cuando se regresan finos de cemento al concreto en aguas de enjuague recicladas, se pueden tolerar 50,000 ppm.
Agregado para concreto
Los agregados finos y gruesos ocupan comúnmente de 60% a 75% del volumen del concreto (70% a 85% en peso), e influyen notablemente en las propiedades del concreto recién mezclado y endurecido, en las proporciones de la mezcla, y en la economía. Los agregados finos comúnmente consisten en arena natural o piedra triturada siendo la mayoría de sus partículas menores que 5mm. Los agregados gruesos consisten en una grava o una combinación de grava o agregado triturado cuyas partículas sean predominantemente mayores que 5mm y generalmente entre 9.5 mm y 38mm. Algunos depósitos naturales de agregado, a veces llamados gravas de mina, rió, lago o lecho marino. El agregado triturado se produce triturando roca de cantera, piedra bola, guijarros, o grava de gran tamaño. La escoria de alto horno enfriada al aire y triturada también se utiliza como agregado grueso o fino.
1): Un material es una sustancia sólida natural que tiene estructura interna ordenada y una composición química que varía dentro de los límites muy estrechos. Las rocas (que dependiendo de su origen se pueden clasificar como ígneas, sedimentarias ko metamórficas), se componen generalmente de varios materiales. Por ejemplo, el granito contiene cuarzo, feldespato, mica y otro cuantos minerales; la mayor parte de las calizas consisten en calcita, dolomita y pequeñas cantidades de cuarzo, feldespato y arcilla. El intemperismo y la erosión de las rocas producen partículas de piedra, grava, arena, limo, y arcilla.
El concreto reciclado, o concreto de desperdicio triturado, es una fuente factible de agregados y una realidad económica donde escaseen agregados de calidad.
Los agregados de calidad deben cumplir ciertas reglas para darles un uso ingenieril optimo: deben consistir en partículas durables, limpias, duras, resistentes y libres de productos químicos absorbidos, recubrimientos de arcilla y otros materiales finos que pudieran afectar la hidratación y la adherencia la pasta del cemento. Las partículas de agregado que sean desmenuzables o susceptibles de resquebrajarse son indeseables. Los agregado que contengan cantidades apreciables de esquistos o de otras rocas esquistosas, de materiales suaves y porosos, y ciertos tipos de horsteno deberán evitarse en especial, puesto que tiene baja resistencia al intemperismo y pueden ser causa de defectos en la superficie tales como erupciones.